We provide you the critical tips you need to increase your Innovate’s O2 sensor life, including placement, tuning, and free air calibration.
When tuners shape the air/fuel curve for maximum horsepower and torque, an engine calibration is only as good as the information streaming into their data logger. While wideband oxygen sensors make it possible to precisely monitor an engine’s air/fuel ratio, properly positioning and calibrating the sensor is essential to optimizing accuracy and maximizing sensor longevity. Fortunately, following a few simple guidelines goes a long way to getting the most out of your O2 sensor.
Positioning
Ideally, the O2 sensor should be placed at least 24 inches downstream from the cylinder head exhaust ports. This ensures that the O2 sensor takes its measurements after the exhaust gas from each primary merges into a common collector. In turbocharged applications, the sensor should be placed at least 24 inches downstream of the turbo.
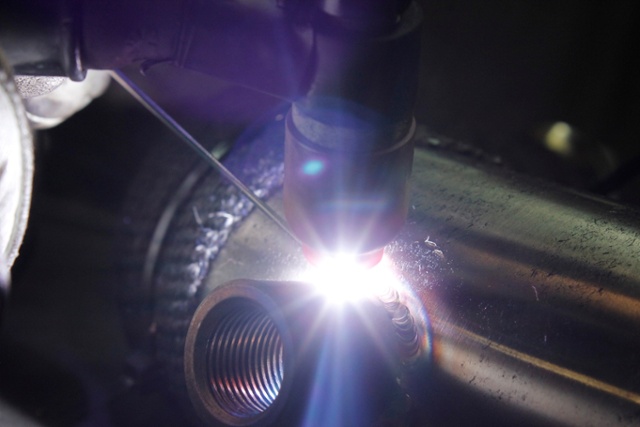
Positioning the sensor too close to the exhaust ports can expose it to high exhaust gas temperature (EGT) as well as over-cooling from the high-velocity exhaust gas flowing over the sensor. Likewise, if an engine runs excessively rich, an oxygen sensor that’s positioned farther downstream is less prone to fouling. Although these extreme conditions aren’t a concern in most street applications, placing the sensor farther down the exhaust tract is rarely detrimental.
In V- and horizontally opposed engines that have two banks of cylinders, the O2 sensor should still be placed at least 24 inches from exhaust ports, but before the H- or X-pipe. “Since most street cars are tuned with a built-in margin of safety, it’s perfectly fine to read the air/fuel ratio off just one bank of cylinders. In race applications where you are competing for every last horsepower, then it becomes more critical to read the air/fuel ratio off both banks of cylinders with one of our dual-channel wideband O2 sensor kits,” Felipe Saez of Innovate Motorsports explains.
While track-only cars equipped with exhaust dumps, cut-outs or open-header exhaust systems can experience false-lean readings at idle and part-throttle, it’s seldom an issue since these applications operate primarily at wide-open throttle. “With these types of competition exhaust systems, free air coming in through the exhaust outlet at idle and part-throttle can contaminate the air/fuel readings. When exhaust pressure increases at WOT, the readings will be accurate once again,” Saez elaborates.
Once establishing how far downstream in the exhaust system to position the wideband O2 sensor, the bung should be mounted between 9 o’clock and 3 o’clock. Condensation buildup can destroy a sensor very quickly, so mounting the sensor between 9 o’clock and 3 o’clock protects it from water build-up at the bottom of the exhaust pipe. If there is sufficient space between the top of the exhaust pipe and floorboard, mounting the sensor at 12 o’clock is ideal.
(Left) To properly calibrate the O2 sensors, they must be hooked up and left in a fresh air environment. (Right) The sensors will toggle to a “CAL” on screen during calibration and then display the current air/fuel ratio.
Free Air Calibrating the O2 Sensors
Since cars are driven in wide variety of climates and altitudes, calibrating a wideband O2 sensor to free air is the only way to ensure accuracy. The Bosch LSU 4.2 and LSU 4.9 wideband O2 sensors utilized in Innovate’s wideband systems rely on a resistor located in the connector to provide proper calibration. Bosch sets these calibrations under lab conditions that simulate 14.7 psi of atmospheric pressure at 68 degrees Fahrenheit.
In order for the factory Bosch calibration to perform at optimal accuracy, a car must be driven at sea level on a 68-degree day. Obviously, the vast majority of performance vehicles operate outside this tiny window, which is why Innovate developed a patented digital wideband sensor controller that allows each and every end user to free-air calibrate their O2 sensors to the actual environment that their cars are driven in.
In addition to the effects of atmospheric pressure variations, O2 sensors wear out over time and become less accurate. According to Bosch’s published test data, its wideband O2 sensors are accurate to .15 of a point when new, but that margin for error increases to .29 after 500 hours of use, and increases even more to .59 after 2,000 hours. In other words, after 2,000 hours of operation, when an O2 sensor reports an 11.76:1 air/fuel ratio, the actual air/fuel ratio in the engine can be as lean as 12.35:1 or as rich as 11.17:1.
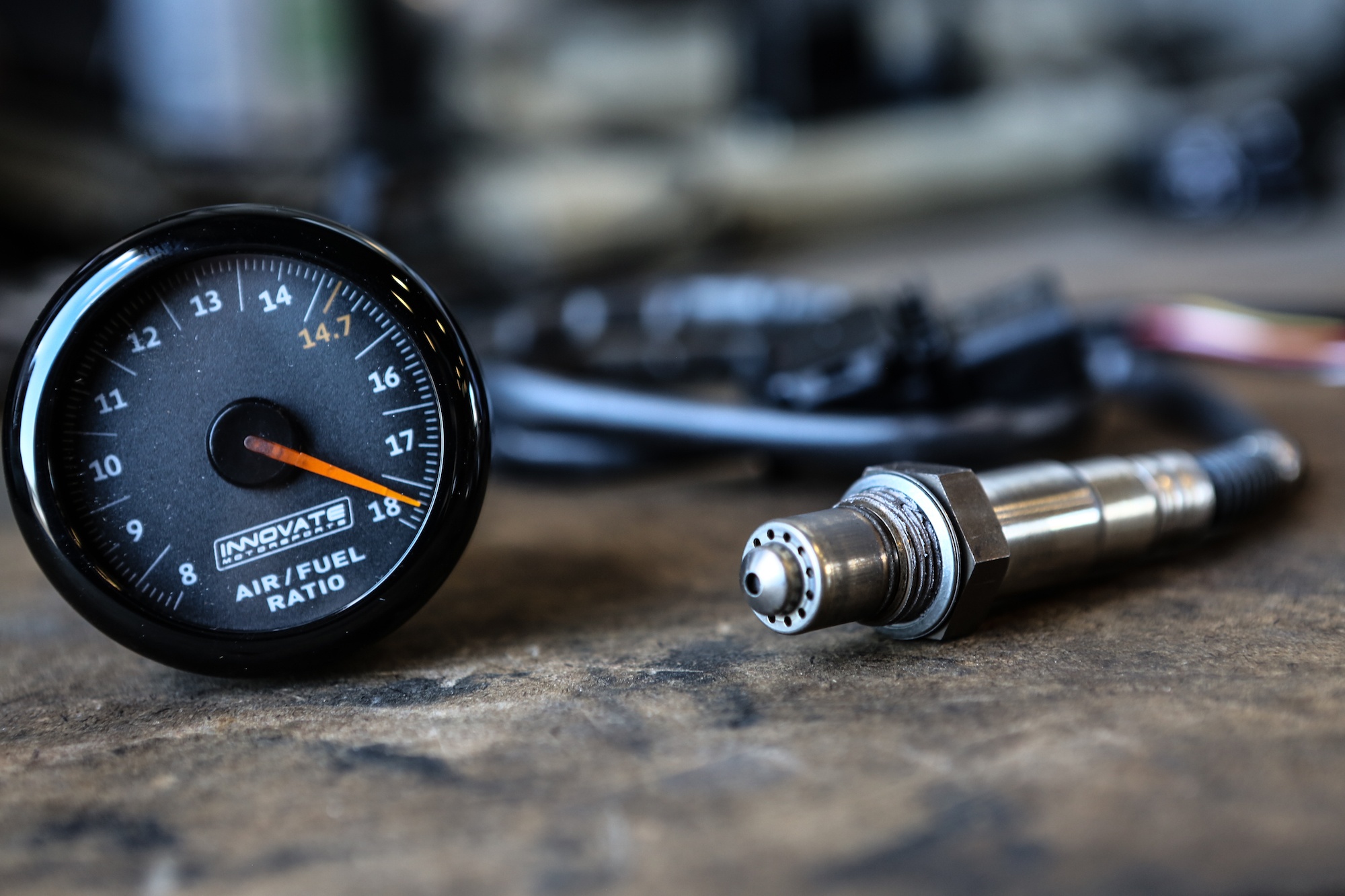
Keep in mind that Bosch conducts its tests under strictly controlled lab conditions. In the real world, O2 sensors wear out much more quickly in performance applications due to elevated EGTs and richer air/fuel ratios. Detergents and additives commonly found in pump fuel accelerate sensor wear as well. Just like Innovate’s digital wideband sensor controller can compensate for altitude through free-air calibration, this same technology can be used to compensate for sensor wear by periodically re-calibrating the sensor as follows.
Naturally aspirated street car | Calibrate immediately after installing new sensor. Re-calibrate after first 3 months. Thereafter, calibrate once per year or every 20,000 miles. |
Forced induction street car | Calibrate immediately after installing new sensor. Re-calibrate after first 3 months. Thereafter, calibrate twice per year or every 10,000 miles |
Race car running leaded fuel | Calibrate immediately after installing new sensor. Re-calibrate every race weekend. |
Dyno use | Calibrate immediately after installing new sensor. Re-calibrate every 2-3 days. |
Altitude changes | If vehicle experiences altitude change of 5,000 feet or more, re-calibrate sensor before competition use. |
Getting the Maximum Life Out of your O2 Sensor
Naturally, O2 sensors are designed to live in an environment full of exhaust fumes. The most common ingredients of tailpipe emissions include nitrogen, carbon dioxide, and water vapor with a hint of carbon monoxide and nitrogen oxides mixed in. In contrast, when anything other than exhaust gas enters the exhaust system, it can dramatically reduce an O2 sensor’s lifespan.
The most common culprits—in descending order of importance—include overly rich air/fuel mixtures, improper sensor placement, leaded fuel, oil consumption, coolant, high-zinc race motor oil, and elevated EGTs. In the event of catastrophic engine failure, where a volatile mix of oil, coolant, fuel and shrapnel can shoot through the exhaust system, an O2 sensor’s lifespan can decline in a hurry.
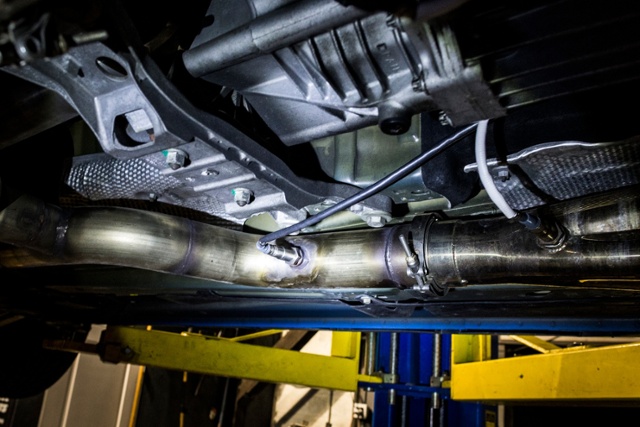
In high-performance street and race applications, it’s simply not practical to completely isolate O2 sensors from all the various elements detrimental to their health. Many high-compression and high-boost motors require leaded race fuel, and elevated EGTs are the norm for turbocharged, rotary, and diesel engines. Likewise, high-zinc motor oils are essential to valvetrain durability in many high performance pushrod applications.
Nevertheless, maintaining a healthy engine with good ring seal and a proper tune is the best way to not only extend the performance and durability of the engine itself, but the longevity of the O2 sensors as well. “The main things to focus on are proper sensor placement and the engine tune. Everything else is secondary,” says Saez.